開発の背景と経緯
- イチゴ生産は10a当たり約2,000時間を要し、その約3割が選別パック詰め作業に費やされています。選別パック詰め作業は果実を傷つけないように人手
で丁寧に扱う必要があり、機械化が進んでいませんでした。そのため、選別パック詰め作業は収穫作業と同様に規模拡大の大きな阻害要因となっています。
- そこで、生研センターでは収量当たりの労働時間半減を目標とする「担い手プロ」の中で、平成19年4月から選別パック詰め作業の自動化に向けた研究開発に着手しました。
- 平成20年までに果実の大きさ・形状・着色度合を判別する画像処理技術と、果実を傷つけないように取り扱うハンドリング技術を開発しました。平成21年に
これらの技術を統合して果実を大きさ別に分け、専用の通い容器に収容する自動選別パック詰め装置のプロトタイプを試作しました。
- 平成22年には、通い容器だけではなく市場で流通している平詰めソフトパックにも対応できるように改良しました。さらに、平成23年には、収穫箱から果実を取り出して装置に自動で供給する機能を追加し、佐賀県で実証試験を行いました。
開発機の概要
- 作業者は、収穫箱と出荷容器のセットを行うだけで、果実取り出しから、選別、パック詰めまでの作業を装置が自動的に行います。パック詰めは専用の通い容器と平詰めソフトパックに対応しています。
- 装置は、収穫箱から果実を取り出して1個ずつ果実搬送コンベア上に置く供給ユニットと、供給された果実を選別してパック詰めする選別ユニットから構成されます(図1)。専用の通い容器、あるいは平詰めソフトパックは、出荷容器搬送コンベアで搬送されます。
- 供給ユニット(図2)では、デジタルカメラにより収穫箱内に散在する果実を検出し、吸着ハンドで1個ずつ吸着し、間欠運転する果実搬送コンベア上に順々に置いていきます。吸着ハンドは果実を傷つけないよう、イチゴを押し付けずにソフトに吸着する構造としています。
- 選別ユニット(図3)では、カメラ画像により得られた果実の大きさから果重を推定し、さらに、果実方向を検出することで得られた果底(ヘタ)部を、4軸マ
ニピュレータに装着された吸着ハンドで吸着し、大きさ別に出荷容器に向きを揃えて並べます(図4)。比較的硬度が高い果底部を吸着するので、ほとんど損傷
なくハンドリングできます。
- 「さがほのか」の選別パック詰め作業におけるハンドリング成功率は97%、果実1果当たりに要する作業時間は約7秒と慣行の手作業と同等の能率でした。また、画像処理による果重の推定誤差は±2gに収まりました。
活用面と留意点
- 3Lに相当する果重30g以上になるとハンドリング成功率が徐々に低下し、40g以上の果実はハンドリングできません。
- 果実取り出し精度を向上させるため、果実を認識しやすいように収穫箱底面の緩衝材は黒色とする必要があります。
今後の予定・期待
本研究で開発したハンドリング技術が「イチゴパック詰めロボットの開発」(農業機械等緊急開発事業:平成23~25年度)に活用されています。
用語の解説
デジタルカメラ
本文でいうデジタルカメラは、カメラと照明から構成される画像撮影ユニットです。供給ユニットでは、果実領域の明るい部分の重心を吸着位置として算出し
ます。選別ユニットでは、果実領域の画素数から果重を推定する他、果実領域のヘタ部と赤色部の位置から果実方向を求めます。
吸着ハンド
マニピュレータ先端に取り付けられ、果実を吸着します。0.05~0.07kg/cm2(5~7kPa)程度の負圧で吸着し、圧力センサで吸着の有無を確認します。
専用の通い容器
洋菓子店などの実需者を対象として、繰返し使用する出荷容器です。果実サイズにより48~75果収容可能で、通常の2段詰めパックと比較して輸送・貯蔵時の果実損傷割合が小さいことが農研機構・近畿中国四国農業研究センターの調査で分かっています。
平詰めソフトパック
凹みがある発泡ポリエチレン製の出荷容器です。流通時の果実損傷が少ないことが報告されています(中村宣貴・他、農業施設、39(1)、1-8.)。
ハンドリング成功率
全供試果実数に対し、収穫箱から取り出され、出荷容器の所定の位置に置かれた果実数の割合です。果実を拾い上げられなかったり、果実を落とす他、果実を認識できない場合などに低下します。
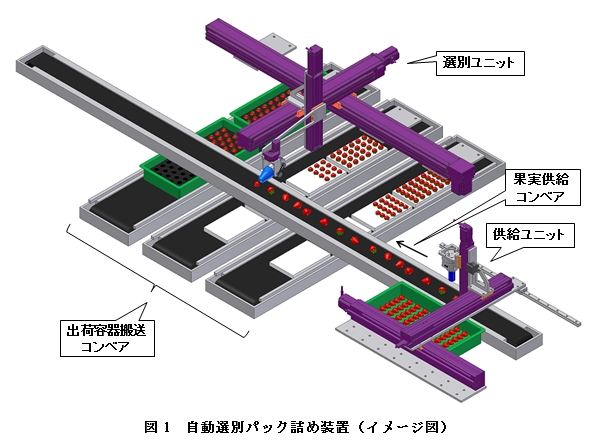
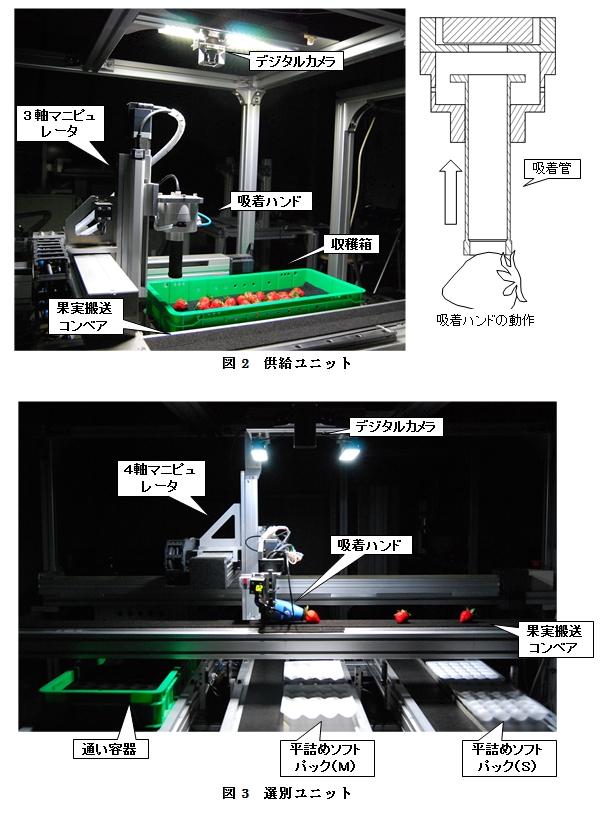
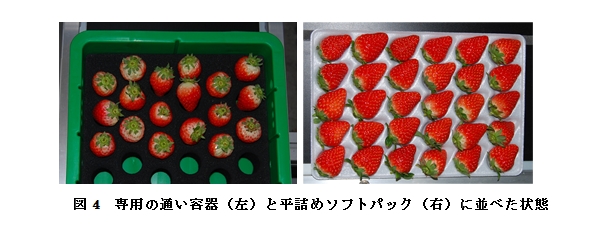